(PART 1 of 5)
This post is about the lightning protection system (LPS) I built for my ground mount solar system that has four ground mounts using the Iron Ridge XR1000 rail system and Robbinslightning components. All total the system has thirty-two XR1000 rails with 8 rails on each mount with a total of 80 260W panels and 80 Enphase microinverters.The result is a fully compliant NFPA 780 LPS that followed the additional guidelines in LPI 175.
Note that I have not received any financial benefit from this work - nothing from either Robbinslightning nor Ironridge or any other company or business. All of this information is provided as-is and is my opinion only. My purpose in posting this is to show how I designed my LPS system and hopefully will be a starting guide to other DIY'ers.
This post is mostly specific to ground mount solar systems. Rooftops solar systems have additional considerations for LPS not discussed here in that you are protecting the entire structure - not just the solar system.
This is a BBCode version of my Google Blogger post which I had to create by hand - cutting and pasting text and rebuilding image URL's. Images come from a public Flicr folder since Google Photos public URL's tend to have time limits. Time permitting I will try and keep this one up-to-date but the master document can be found at the blog site in my profile. Also note that forum software would not let me make this a single post thus I had to break it up into 4 posts due to the number of images.
LPS are defined under NFPA 780 but additional information is from LPI 175. Both specs provide extensive additional information and are the best place to start if researching a LPS. From there one can find many research studies and not surprisingly the military has some of the best studies, an older unclassifed example is here: http://www.dtic.mil/dtic/tr/fulltext/u2/a261900.pdf
NFPA 780 is organized in the the following sections.
When starting off, I would recommend reading LPI 175 General section, then NPFA 780 Annex B and C, and then read 780.12 and then go dive into the extensive material in 780.4. When you get into the ground and bonding subsections, switch back over to LPI 175 and read the Grounding and Bonding sections.
One thing that must be brought up is the cost-benefit of a LPS. 780 annex L is all about the risk assessment to understand both the actual risk and financial costs/benefit of a LPS. This includes possible insurance benefits or even requirements. For DIY'ers one may decide that a LPS provides additional personal time insurance against repairs that may be required in the future. My purpose is just to bring this topic up and individuals have to decide for themselves if the cost and time to install justify the possible reduced damage savings.
There are two main risks to a ground solar system from lightning. First and least common is a direct hit or splash hit. This most likely will be catastrophic to a unprotected system - inverters blown due to internal shorting and panels made inoperative from either physical or electrical damage. From the studies I found, direct hits tend to cause damage to all panels in the array. This is a rare event but could result in extensive replacements. In addition, lightning can be castrostic to concrete - the large currents can vaporise the internal water and cause concrete to crack and even explode.
http://www.solarpowerworldonline.com/2015/03/lightning-protection-for-solar-panels-protects-your-investment/
http://www.30north.com.au/node/129
http://www.30north.com.au/node/128
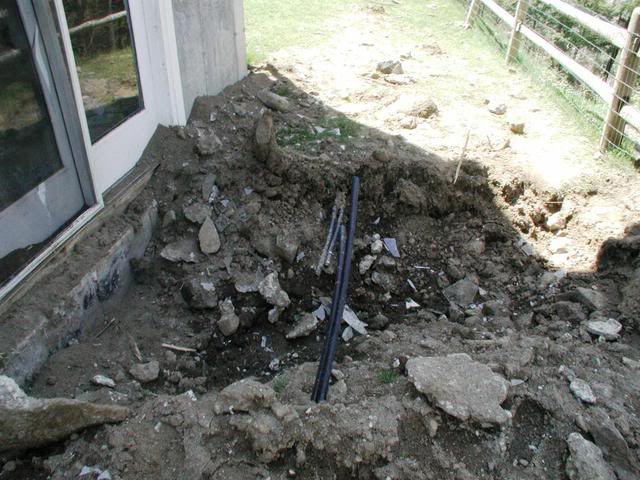
Far more common is a near strike. This will cause a large voltage gradient in the soil and anything grounded will pick up that voltage gradient. This is what makes 690.47(D) so dangerous to a house - having multiple ground points with large voltage potential differences leads to side flashing and possible fires. For a ground mount, side flashing could wipe out panels (diodes) and inverters (shorting) and can even explode PVC boxes.
This is all that is left of a PVC box on my front driveway electric gate from a lightning event a couple of years ago. Shorting inside the box heated the moist air causing it to explode - and is a good reason to not use any PVC above ground when possible.. This event also completely destroyed the gate controller box (PVC) and electronics - the parts of the cover were found 30' away, the gate motor fried, and exploded a 120v to 24v transformer in my pump house 80' away leaving nothing but small pieces of metal and plastic everywhere. It damaged the GFCI wall socket it was plugged into.
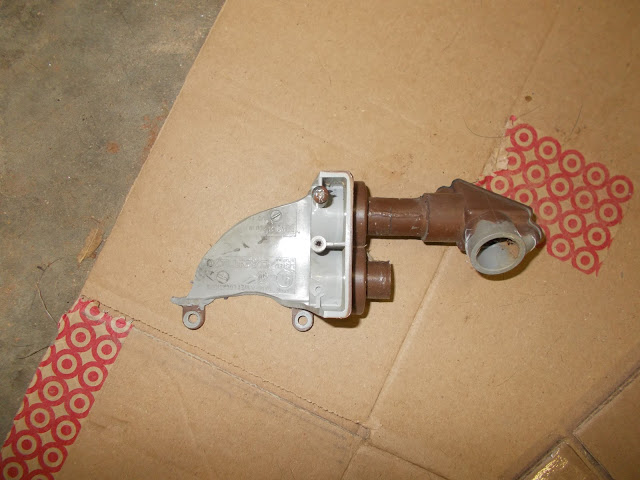
There are many articles about partial damage from lightning. Not surprisingly, much of the research from this come from the insurance industry and of course the military. A lightning event happens and everything continues to work. Later the system fails. Was it due to partial surge from the prior lightning event? There are a number of research studies trying to quantify this but one runs into the issue of assigning the underlying cause.
The purpose of a lightning protection system for a ground mount has two major concerns - to protect against extensive damage from a direct hit and to protect against side flashing from voltage gradients. It is important to note that lightning is a chaotic event and LPS systems work on a probability - NFPA 780 claims that there is 98% probability of a direct hit being directed into the ground ring - but that means you have 2% chance of an event being completely uncontrolled and splashing anywhere and causing damage.
Lightning protection systems for solar ground mounts comprise of three main parts.
This post is about the lightning protection system (LPS) I built for my ground mount solar system that has four ground mounts using the Iron Ridge XR1000 rail system and Robbinslightning components. All total the system has thirty-two XR1000 rails with 8 rails on each mount with a total of 80 260W panels and 80 Enphase microinverters.The result is a fully compliant NFPA 780 LPS that followed the additional guidelines in LPI 175.
Note that I have not received any financial benefit from this work - nothing from either Robbinslightning nor Ironridge or any other company or business. All of this information is provided as-is and is my opinion only. My purpose in posting this is to show how I designed my LPS system and hopefully will be a starting guide to other DIY'ers.
This post is mostly specific to ground mount solar systems. Rooftops solar systems have additional considerations for LPS not discussed here in that you are protecting the entire structure - not just the solar system.
This is a BBCode version of my Google Blogger post which I had to create by hand - cutting and pasting text and rebuilding image URL's. Images come from a public Flicr folder since Google Photos public URL's tend to have time limits. Time permitting I will try and keep this one up-to-date but the master document can be found at the blog site in my profile. Also note that forum software would not let me make this a single post thus I had to break it up into 4 posts due to the number of images.
LPS are defined under NFPA 780 but additional information is from LPI 175. Both specs provide extensive additional information and are the best place to start if researching a LPS. From there one can find many research studies and not surprisingly the military has some of the best studies, an older unclassifed example is here: http://www.dtic.mil/dtic/tr/fulltext/u2/a261900.pdf
NFPA 780 is organized in the the following sections.
- 780.3 - Definitions.
- 780.4.- The guts of the spec broken into many subsections.
- 780.12 - Solar.
- 780.A - Annex A explanatory material - a wonderful resource that answers "why".
- 780.B - Annex B discusses the theory and physics of lightning protection.
- 780.C - Annex C Explanation of the Bonding Principles.
- 780.O - References - The definitive list of the body of work associated with LPS.
When starting off, I would recommend reading LPI 175 General section, then NPFA 780 Annex B and C, and then read 780.12 and then go dive into the extensive material in 780.4. When you get into the ground and bonding subsections, switch back over to LPI 175 and read the Grounding and Bonding sections.
One thing that must be brought up is the cost-benefit of a LPS. 780 annex L is all about the risk assessment to understand both the actual risk and financial costs/benefit of a LPS. This includes possible insurance benefits or even requirements. For DIY'ers one may decide that a LPS provides additional personal time insurance against repairs that may be required in the future. My purpose is just to bring this topic up and individuals have to decide for themselves if the cost and time to install justify the possible reduced damage savings.
There are two main risks to a ground solar system from lightning. First and least common is a direct hit or splash hit. This most likely will be catastrophic to a unprotected system - inverters blown due to internal shorting and panels made inoperative from either physical or electrical damage. From the studies I found, direct hits tend to cause damage to all panels in the array. This is a rare event but could result in extensive replacements. In addition, lightning can be castrostic to concrete - the large currents can vaporise the internal water and cause concrete to crack and even explode.
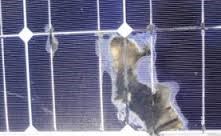
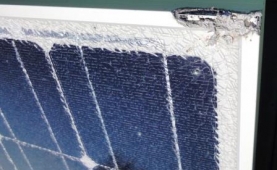

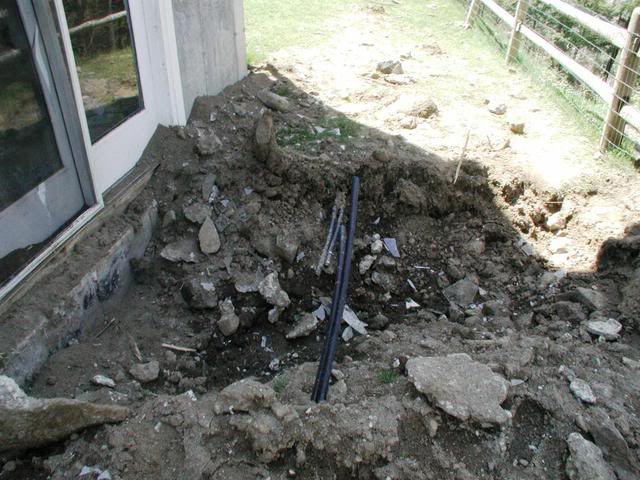
Far more common is a near strike. This will cause a large voltage gradient in the soil and anything grounded will pick up that voltage gradient. This is what makes 690.47(D) so dangerous to a house - having multiple ground points with large voltage potential differences leads to side flashing and possible fires. For a ground mount, side flashing could wipe out panels (diodes) and inverters (shorting) and can even explode PVC boxes.
This is all that is left of a PVC box on my front driveway electric gate from a lightning event a couple of years ago. Shorting inside the box heated the moist air causing it to explode - and is a good reason to not use any PVC above ground when possible.. This event also completely destroyed the gate controller box (PVC) and electronics - the parts of the cover were found 30' away, the gate motor fried, and exploded a 120v to 24v transformer in my pump house 80' away leaving nothing but small pieces of metal and plastic everywhere. It damaged the GFCI wall socket it was plugged into.
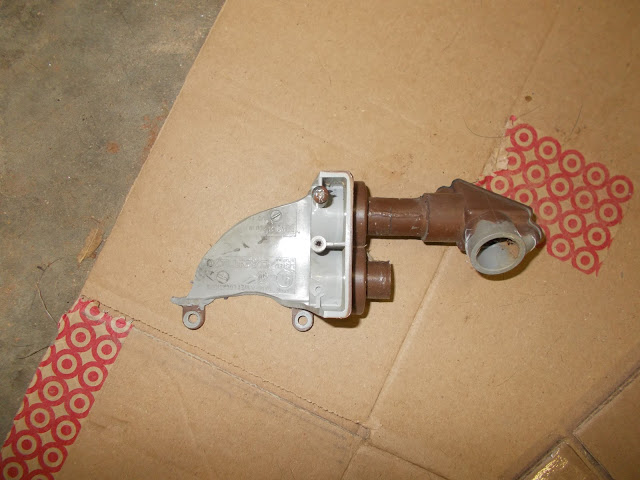
There are many articles about partial damage from lightning. Not surprisingly, much of the research from this come from the insurance industry and of course the military. A lightning event happens and everything continues to work. Later the system fails. Was it due to partial surge from the prior lightning event? There are a number of research studies trying to quantify this but one runs into the issue of assigning the underlying cause.
The purpose of a lightning protection system for a ground mount has two major concerns - to protect against extensive damage from a direct hit and to protect against side flashing from voltage gradients. It is important to note that lightning is a chaotic event and LPS systems work on a probability - NFPA 780 claims that there is 98% probability of a direct hit being directed into the ground ring - but that means you have 2% chance of an event being completely uncontrolled and splashing anywhere and causing damage.
Lightning protection systems for solar ground mounts comprise of three main parts.
- Ground Ring Electrode and below ground bounding.
- Strike points, down conductors and above ground bonding.
- Surge Protection.
Comment